|
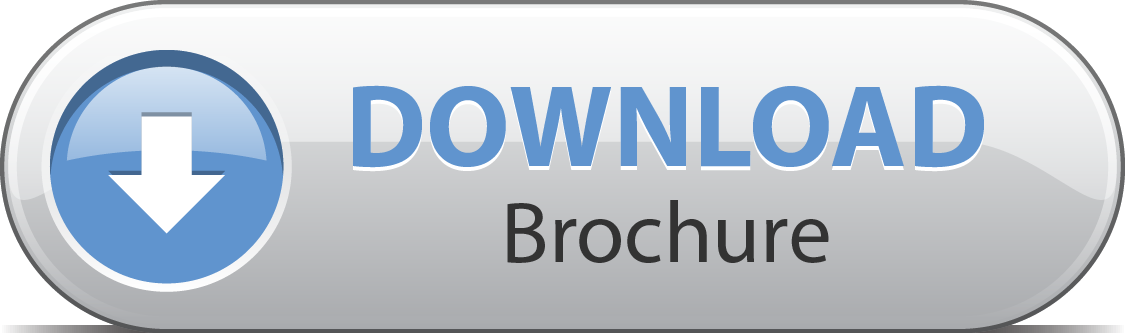 |
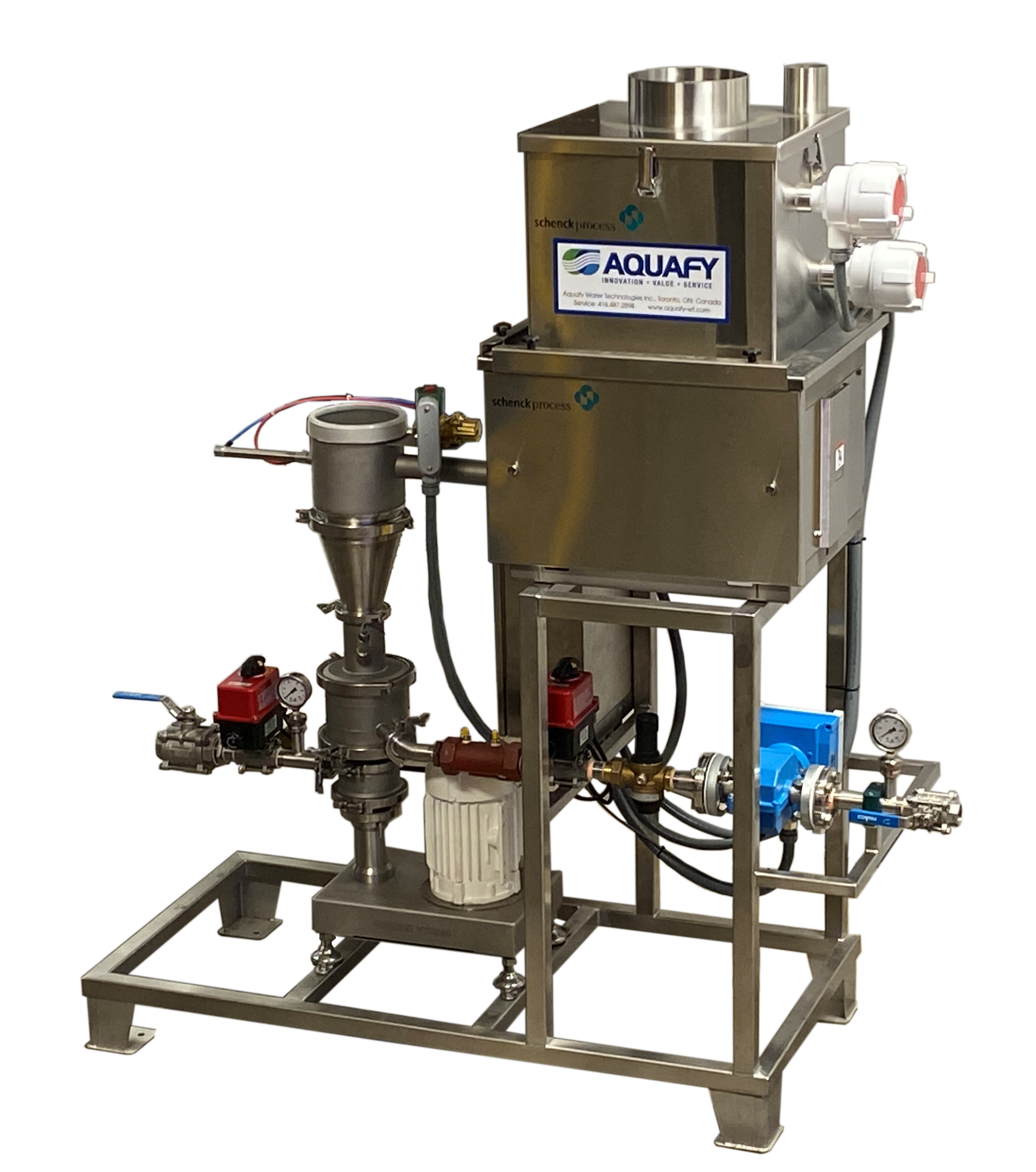 |
AQUAFY DRY POLYMER MAKEDOWN & FEED SYSTEMS
Aquafy Water Technologies Inc. (Aquafy) offers dry polymer makedown and feed systems for the Municipal and Industrial water and wastewater treatment industries. With over 15 years of design and practical hands-on experience, Aquafy can offer innovative solutions for your polymer system project. The dry polymer makedown equipment is designed to efficiently prepare a dry polymer solution with no polymer wastage. Enhanced process performance, reduced water and energy demand, and minimal chemical consumption are the direct benefits.
Our services include: Design Assistance, Preliminary Design and Budget Proposals, Detailed Design Proposals, Submittal Preparation, Submittal Review, O&M Manual Preparation, Start-Up, Commissioning, Training, and Aftermarket Services.
Aquafy provides a complete turnkey system, working with designers and end users to customize the dry polymer system for a specific need.
|
|
SLT Jet Stream Assisted Ultra Polymer DisperserAt the heart of the Aquafy dry polymer system is the Solid-Liquid Turrax (SLT) Jet Stream Assisted Ultra Polymer Disperser unit. The SLT disperser unit uses high shear mixing technology and is especially designed for incorporating and homogenizing the most difficult powders, even at high concentrations. The SLT generator tip speed of approximately 23 m/s ensures dry polymer particles are efficiently dispersed in the dilution water. The proven SLT rotor-stator designs are interchangeable for maximum flexibility. Aquafy offers the widest range of flows in the dry polymer wetting industry ranging from 1.5 to 550 gpm.
By effectively dispersing dry polymer powder into the dilution water flow, “fish-eyes” and agglomerations are prevented. Preventing polymer wastage ensures polymer consumption is reduced resulting in a lower operating cost. Furthermore, by minimizing the polymer particle sizes, the rate of hydration (mix time) is reduced considerably according to the following formula:
Rate of Polymer Hydration α (Polymer Particle Radius)2
The need for aging (defined as the time between when mixing stops and feed to process begins) is completely eliminated reducing the overall batch time. Proper polymer dispersion also allows for the ability to makedown the polymer to at least 1%. This allows for less potable water consumption (post dilution can occur with non-potable water), smaller tanks, smaller mixers, smaller feed pumps, and an overall smaller system footprint. Dry polymer eductor and wetting head technologies cannot generate the same mixing energy and therefore cannot achieve the same level of dispersion. The negative consequence is agglomerations, which can lead to plugging, polymer wastage and subsequent increase in polymer consumption. Furthermore, these systems are limited to makedown concentrations in the 0.1 – 0.5% range and require much longer hydration times and aging. A significant increase in system footprint and potable water consumption results.
The SLT system completely separates the powder zone and the liquid zone. This eliminates water splashing and the resulting build-up of polymer gels on the walls of the mixing chamber. Furthermore, the powder only enters the dilution water stream at the high mixing energy zone and not upstream, which can result in the formation of agglomerations. The water is introduced into the mixing zone through interchangeable spray nozzles, adding to the polymer dispersion phenomenon.
The dilution water flow entering the SLT disperser is a known and controlled flow, thereby ensuring a known, repeatable polymer concentration exiting the SLT. The solution discharging the SLT enters a mix tank(s) whereby it is mixed for a preset amount of time to complete the hydration process. Following the mixer time out, the polymer solution is ready to feed to process.
|
|
Validation of Polymer Hydration
Aquafy offers systems used to validate polymer hydration. The non-proprietary design uses an inline viscometer to continuously measure the polymer viscosity over the course of a batch. A PLC automates the process and data logs a viscosity versus time curve for every batch. The information produced validates that the mix times are sufficient, optimizing the polymer makedown process, improving process performance, and reducing chemical cost.
|
|
Dry Polymer Feeder and Storage Hopper
The Brabender FlexWall® Plus feeder is capable of reliably and accurately metering dry polymer. The feeder has the following main components: a stainless steel trapezoidal exterior, a flexible polyurethane hopper with external massage paddles, a feed screw, a feed screw tube, a
3 phase AC motor and commonly a trapezoidal extension hopper for ingredient storage. Extension hoppers are available with a 1.8 ft³ or 2.5 ft³ volume. Larger hoppers are also available. These components work together to provide consistent screw filling and mass flow of ingredient without degradation since the trapezoidal hopper shape naturally induces ingredient flow and the motor driven (amplitude adjustable) paddles flex the polyurethane hopper walls to promote ingredient flow into the screw. All service is from the front or back. Optionally, the screw removal can be from the rear with a hinged drive motor.
A clear extension tube connects the powder feeder discharge to the top of the SLT disperser. It is easily removable for calibration purposes and is used to observe the powder feed.
|
|
Mix and Day TanksCombined with the dry polymer wetting capacity of the SLT disperser, the tank volumes determine the overall dry polymer makedown capacity of the batch system. Various tank volumes are available depending on the quantity of dry polymer required per hour. For smaller systems, the tanks are stacked. One mix tank sits atop one day tank. The transfer is via a dump valve controlled from the master PLC control panel. The design is such that the day tank never runs empty and therefore continuous polymer solution feed to process is possible. Larger systems incorporate two mix tanks, which operate in a “flip-flop” arrangement. One tank operates as the mix tank while the second tank operates as the day tank. When the day tank empties, the tank operations “flip” and the mix tank is now the day tank. Using stacked tanks and side by side tanks eliminates the need for a transfer pump.
Standard tank materials are 304 stainless steel. Standard tank configurations are cylindrical. Other options are available. All mixers used in the preparation of polymer solution are low shear, low rpm mixers to ensure no damage to the polymer molecules as they hydrate.
|
|
Bulk Bag FrameFor larger applications, dry polymer is supplied in bulk bags to minimize manual refilling of the polymer hopper. The bulk bag is supported in a frame and feeds into the hopper above the powder feeder. Two basic configurations are available. For facilities that are able to use an existing monorail/hoist system or a forklift to lift and move the bulk bag, a frame designed to support the removable bag lifting/holding device is supplied. For other facilities, the bulk bag frame comes with a mounted cantilevered I-beam and dedicated electric hoist and trolley. The bulk bag is lifted into place and supported overtop of the hopper by the hoist. A safety platform separates the bulk bag from the hopper. A 12 inch diameter iris valve with poly-nylon diaphragm is used to safely open, close, and control flow from the bulk bag outlet spout. The iris valve has a fully notched, cast aluminum body that allows for incremental valve positioning and is manually opened and closed with a hand lever.
The frame posts are easily adjustable in small increments to accommodate bags of all popular heights.
Materials of construction include structural mild steel (primed and painted) or 304 stainless steel.
|
|
Control PanelThe Aquafy dry polymer makedown system comes with a PLC based control panel with touch screen colour HMI. The control panel operates the complete polymer makedown system including the SLT polymer disperser, the powder feeder, all valves, the mixer(s), and any other device that is part of the makedown system operation. All components can be operated manually (for start-up and maintenance) off of the HMI. In auto mode, the system operates in a batch sequence ensuring polymer solution is always available to feed to the process. Screens are available for system status, component/system operation mode, powder feeder calibration, timer settings, run time/totalizers, and alarms.
Control panel customization to suit the customers design and component preferences is also available.
|
|
Polymer Solution Feed PumpsAquafy offers complete skid mounted Polymer Solution Feed Pump Systems. Our standard offering is suitable for day tanks storing the final feed polymer concentration. The package includes progressive cavity pumps with run dry protection, pump pressure relief valves, pump overpressure protection, isolation ball valves, check valves, electromagnetic flowmeters, and a VFD control panel all pre-mounted, pre-piped, and pre-wired for a complete turnkey system. When the day tank stores concentrated polymer solution, Aquafy offers a post dilution option to reduce the polymer concentration fed to process. Post dilution includes a water inlet solenoid valve, a manual water control valve, a rotameter, and a static mixer all controlled from the control panel. Adding a modulating water control valve, an electromagnetic flowmeter, and a PLC will allow this option to produce a constant polymer concentration to process.
The feed systems, which are fully customizable, can be built to customer specifications.
Aquafy partners with a quality systems builder to ensure the highest quality of equipment designed to last. With over 45 years of combined fabrication experience, the workmanship is second to none. Experience ensures that components are easily accessible by operation and maintenance staff and laid out in a logical manner. Factory testing of all equipment allows for customer piece of mind.
The systems builder is a TSSA certified facility. The certified piping fabricators are required to undergo a welding certification test annually to renew their qualifications to assure their skills meet the guidelines set forth by TSSA and ASME. The benefits of utilizing a TSSA certified facility includes: quality assurance through stringent documentation control throughout the fabrication process; all pressure piping is constructed to the ASME and CSA B51 pressure piping code; upon completion of the fabricated piping, every pressure piping section is hydrostatically tested and witnessed by a TSSA authorized inspector; quality control program developed in accordance with ASME B31.1 Power Piping, ASME B31.3 Process Piping, and CSA B51 Boiler, Pressure Vessel and Pressure Piping codes, which is monitored by TSSA; 100% visual examination of all fabricated items, with Non-Destructive Examination (NDE), Radiography (X-ray) Examination for Groove or “Butt” Welded joints, and Positive Material Identification (PMI) also available.
|