|
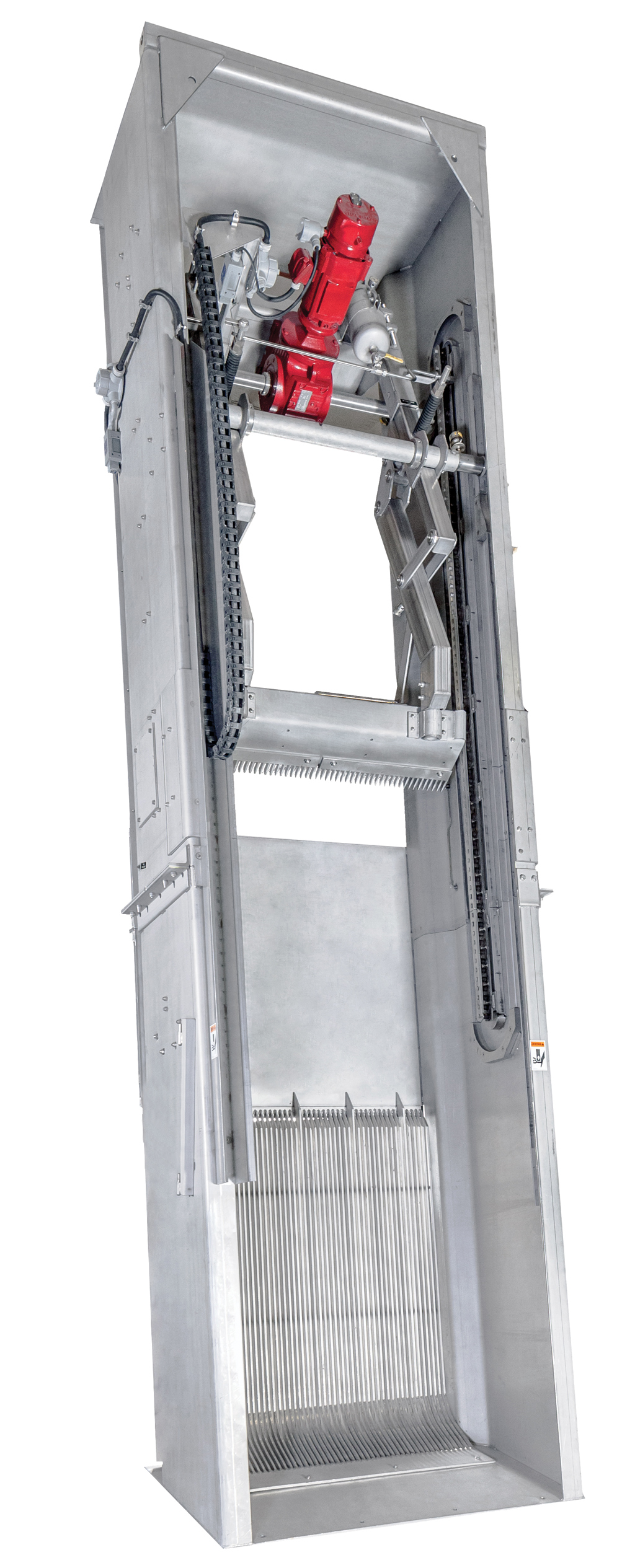 |
MENSCH SEVERE DUTY
The Mensch Severe Duty™ Bar Screen is well known
for its versatility in a wide array of pumping station and
head works projects, along with setting the standard
for robust design in the most severe waste water,
combined sewer, and storm water applications.
You cannot find a more durable screen on the market.
Mensch Bar Screens are custom designed and
fabricated to meet the demands of the environment
in which they are placed. All frame, bar rack, and
drive components are sized according to severe duty
design standards that ensure every screen performs
to the full satisfaction of the client in every application.
There is no comparison in quality and service after
the sale. With over 2000 installations operating in the
United States alone, Vulcan is the leader in severe
duty bar screen applications.
|
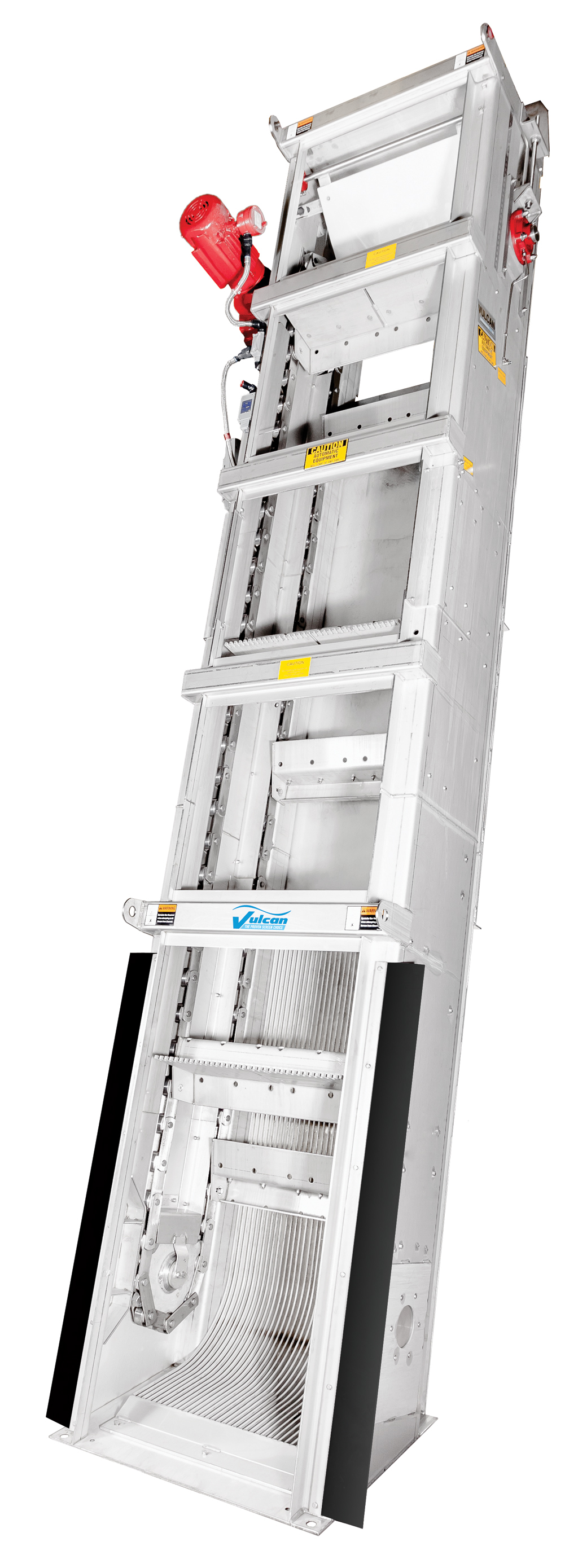 |
VMR MULTI-RAKE SCREEN
Since 1978, Vulcan has been a leader in manufacturing
quality wastewater equipment. The VMR Multi-Rake
Screen continues this tradition of excellence, incorporating
many of the same features found in our Mensch Severe
Duty™ Bar Screen. Coupling these tried and true features
with Vulcan’s own UL approved fully automatic and
multiple speed controls produces quick and efficient
screenings removal.
Designed for use in high screenings volume applications,
the VMR Multi-Rake Screen can efficiently remove large
amounts of screenings with continuous operation. The
versatility of the VMR Multi-Rake Screen makes it ideal for
special applications of extreme channel depth and severe
screen blinding. Heavy duty components used in the VMR
Multi-Rake Screen ensure a long and productive service
life even under the most severe conditions.
The VMR Multi-Rake screen is an automatic, self-cleaning
mechanical bar screen designed for tough primary and
secondary screening applications.The VMR Multi-Rake Screen can be customized for new
construction as well as existing channels.
|
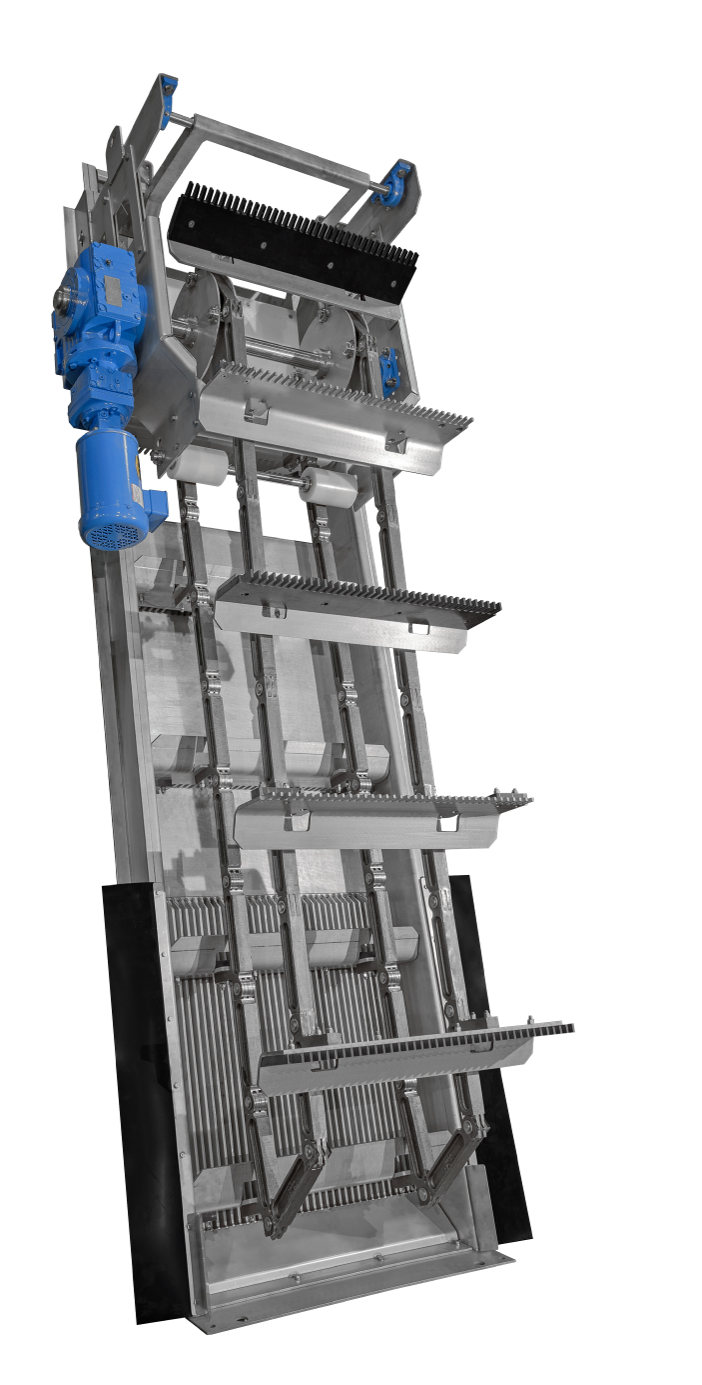 |
MODEL VKR KNUCKLE-RAKE BAR SCREEN
The VKR Knuckle-Rake Bar Screen is a budget
and maintenance friendly screen intended for many years
of care-free service. The VKR Screen is an automatic,
self-cleaning mechanical bar screen customized for
existing and new construction with bar openings
1/4-inch and larger.So what’s different? The Model VKR Knuckle-Rake Bar
Screen uses a unique knuckle chain link that only bends
in one direction. This allows engagement of the rake teeth
into the bar rack by the knuckle link design forming its
own lower turn-around without a sprocket or guide rail
system in the flow. The knuckle link design allows the
rake heads to disengage from the bar rack should a large
object be encountered or an object is lodged in the bar
rack. However, to ensure an adequate force still exists to
dislodge material in the bar rack, Vulcan placed a high
level of importance on the link design. For this reason,
Vulcan casts the links to weigh 6 pounds; an improvement
of 33 percent over the competition. This is extremely
important for a screen that relies on the weight of the
links and rake heads to maintain rake head engagement
into the bar rack. We want the rake heads to disengage to
remove large material, but we also want to ensure tooth
penetration doesn't suffer when blinding occurs. Each
rake head is provided with rake teeth so that every rake
head engagement cleans the three sides of the bar rack
bars exposed to the screenings. No flat head “staging”
scraper used (or needed).
Rake head shapes control where the screenings end up.
VKR rake heads are formed with a scoop shovel shape
to contain the screenings collected from the bar rack.
That way, screenings are kept on the rake head until the
rake wiper removes them automatically. This reduces the
amount of screenings falling back into the flow or onto the
operating floor.
|
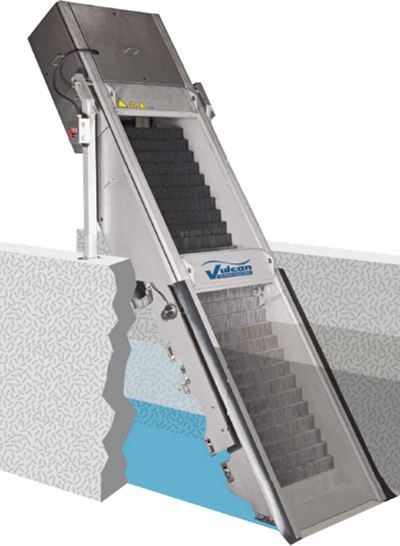 |
MODEL ESR STAIR SCREEN
The Model ESR Stair Screen is an automatic, self cleaning, fine screen for primary, secondary or sludge
screening in municipal and industrial sewage treatment installations. The screens are also ideal for industrial
applications such as slaughterhouses, tanneries, breweries, and paper plants. The design of the Model ESR
Stair Screen allows for easy installation in new and existing facilities without channel modification. With a
maximum setting angle of 57º, the Model ESR Stair Screen has a compact overall footprint.
The side frames of the Model ESR Stair
Screen are constructed of formed stainless
steel plate having a thickness of 0.24”
(6 mm). The screening elements (aka
lamellas) in the screening area are stainless
steel. The lamellas in the transport area
can be stainless steel or a corrosion
resistant, UV stabilized synthetic material,
depending on the overall height of the
screen. The drive system consists of a
gear reducer, motor, and a dual chain
transmission system with automatic chain
tensioning devices. To prevent corrosion,
ease maintenance and ensure years of
reliable service, the drive system is located
completely above the maximum water
level, and the gear reducer and motor are
encapsulated away from the corrosive
atmosphere of the channel. All moving
parts of the drive system are protected by
removable enclosure panels. The screen
enclosure above the channel are equipped
with removable panels to provide safe
operation and reduce odor.
|
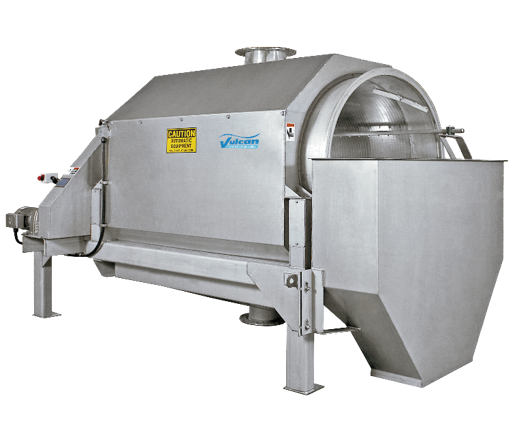 |
LIQUI-FUGE LFP PERFORATED ROTARY DRUM SCREEN
The Liqui-Fuge LFP, Perforated Drum Screen is an
automatic, self-cleaning fine screen for a variety of
applications from primary to membrane screening in
municipal and industrial sewage treatment applications.
This latest rotary drum screen from Vulcan Industries is
specifically designed for protecting secondary and tertiary
wastewater treatment systems. While other treatment
technologies including MBR, IFAS and MBBR systems are
fouled by hair, fibers and small particles, the fine opening
perforated media of the LFP can effectively remove those
materials in normal operation. The Liqui-Fuge LFP is
designed to accept pumped flow and is internally-fed.
The Liqui-Fuge LFP consists of a drum of perforated media,
internal and external spray system, flow distribution tray,
support structure with trunnion wheels, drain pan (when
required), removable enclosures and a drum drive system.
The drum drive system consists of a gearmotor and a
reliable, smooth running cog belt drive that eliminates chain
maintenance. All wetted parts and the support structure
are constructed of either 304 or 316 stainless steel.
|
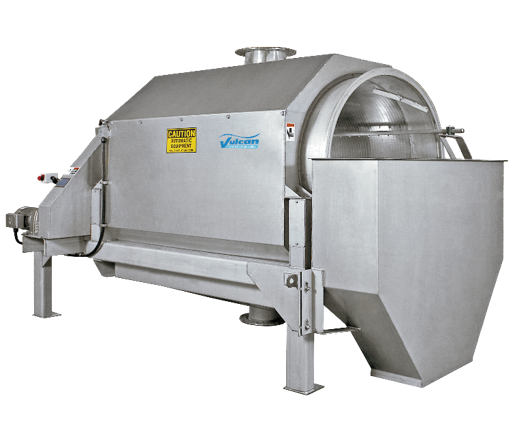 |
LIQUI-FUGE LFS WEDGE-WIRE ROTARY DRUM SCREEN
The Model LFS Liqui-Fuge RDS, rotary drum screen
is an automatic, self-cleaning fine screen for primary
screening in municipal and industrial sewage treatment
applications. The screens are also ideal for industrial
applications such as slaughterhouses, tanneries,
breweries and paper plants. The Liqui-Fuge RDS is
designed to accept pumped flow and is internally-fed.
The Liqui-Fuge RDS consists of a wedge-wire drum,
internal and external spray system, flow distribution
tray, support structure with trunnion wheels, drain
pan (when required), removable enclosures and a
drum drive system. The drum drive system consists
of a gearmotor and a reliable, low maintenance
synchronous drive belt. All wetted parts and the
support structure are constructed of either 304 or 316
stainless steel.
|
|
MODEL SS STATO SCREEN
The Model SS Stato Screen is a non-mechanical screening device for separating solids from liquids. Because there are no mechanical parts and the unit requires no power, these screens can be installed with minimal capital investment. With a wide range of uses the Stato Screen is ideal for municipal waste water and industrial applications.
Available in 304 or 316 Stainless Steel with flanged inlet and outlet pipes. Hinged enclosures, extended discharge chutes and spray systems are available as optional features.
|
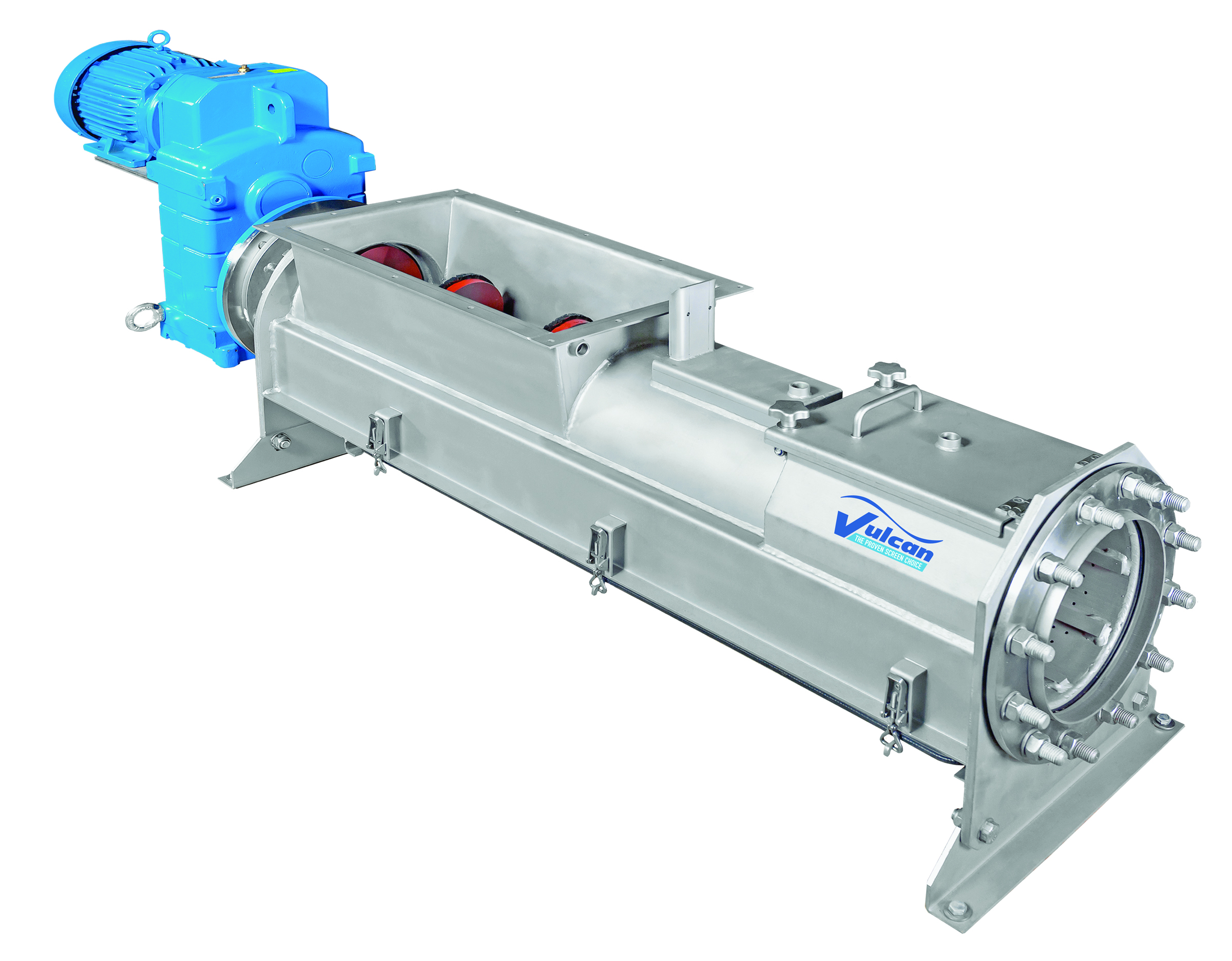 |
MODEL EWP WASHING PRESS
The Model EWP Washing Press is a spiral press used to wash
organic matter out of screenings material. The Washing Press
washes, dewaters, compacts and transports screenings to a
conveyor, container or other suitable receiving device.
The Washing Press consists of a press body with separate washing
and dewatering sections, hollow shaft spiral, axial thrust bearing
(see photo on left), gear reducer and motor, drain pan, washwater
spray connections and sequencing valves.
The press body is constructed of stainless steel. A wedge wire
drain constructed of individual profile bars is mounted on the
bottom of the press and extends from the inlet hopper through
the washing section. The wedge wire, with 2 mm spacings,
guarantees clog-free drainage of the washwater, while ensuring
screenings capture.
The spiral, of alloy steel construction, is welded to the hollow shaft.
The hollow shaft contains perforations located in the washing zone
to introduce washwater to the screenings from the inside out. A
nylon brush is attached to the trailing edge of the spiral to ensure
debris is thoroughly removed from the drainage area. The drain
pan is constructed of stainless steel, and is located directly under
the press body. A flushing nozzle periodically rinses the drain pan.
Sealed with a gasket, and secured with a latching system, the
drain pan is easily removed for service.
|
|
MODEL ESP SCREW PRESS
The Model ESP Screw Press consists of an
axial thrust bearing with a stainless steel body; inlet
hopper; wedge-wire drain; substantial, precision machined
shafted spiral; press housing with compression zone;
flushing nozzle; press water drain pan and drive assembly.
The shafted spiral is cantilevered off the thrust bearing,
and does not rest in the housing. This eliminates metal-tometal
contact during operation.
The profiled bars used in the construction of the wedgewire
drain allows for greater flow than perforated drains and
helps to prevent blinding. A nylon brush is affixed to the
outside edge of the spiral to aide clearing the drain even
when greasy material is present.
|
|
MODEL TF SHAFTLESS SCREW CONVEYOR
The Model TF Shaftless Screw Conveyor is utilized
for the transport of screenings, grit or sludge in
municipal and industrial wastewater treatment
applications.
The conveyor body can be constructed of 304 or
316 stainless steel. The shaftless screw is available
in high-strength alloy steel or stainless steel. The
screw conveyor utilizes a fully enclosed U-trough with
removable covers. The conveyor body is modular
and custom-built for each application. Multiple inlet
hoppers can be provided to allow solids from multiple
sources to be accepted. UHMW polyethylene liners
are mounted in the bottom of the U-trough and fully
support the shaftless screw along its length.
For screenings applications, a compaction head can
be provided on the discharge end of the conveyor to
dewater and reduce the overall volume of screenings.
A water flushing system is provided as an integral part
of the compaction head to ensure that it remains clear
of debris.
|
|
MODEL ESK GRIT CLASSIFIER
The Model ESK Grit Classifier consists of a stainless steel sedimentation tank fitted with flanged inlet and outlet connections, support legs, baffled sidewall with scum board, integrated U-trough with replaceable non-metallic liner, a shaftless spiral and a gear motor drive. The tank is fitted with covers to fully enclose the process liquid and sediments, and a ball valve is installed at the bottom of the tank for draining. Grit cyclones are also available as an integral part of the classifier. Cyclones allow grit classifiers to receive higher flows.
|
|
MODEL ESW-SRW GRIT WASHER
The Model ESW-SRW Grit Washer is used to wash sediment taken from a grit chamber in a sewage treatment plant. The Grit Washer washes and dewaters the sediment and transports the resultant sand particles to a container or conveyor while the organic matter and wastewater is reintroduced into the flow stream.
The Grit Washer consists of a conical shaped tank with support legs, an internal overflow weir with integral drain pipe, mechanical propeller, discharge conveyor with spiral, gear reducer and motor, washwater headers, air headers and pneumatically operated isolation valves.
The tank, overflow weir and discharge conveyor body are constructed of stainless steel. The spiral is shaftless and is constructed of alloy steel. The drive is mounted on the top of the discharge conveyor and the spiral rests on a replaceable liner inside the conveyor so there is no need for a lower bearing.
|
For more information, please click on the logo below.
|
|
|
.jpg) |